Delivery and insertion | Thread cutting |
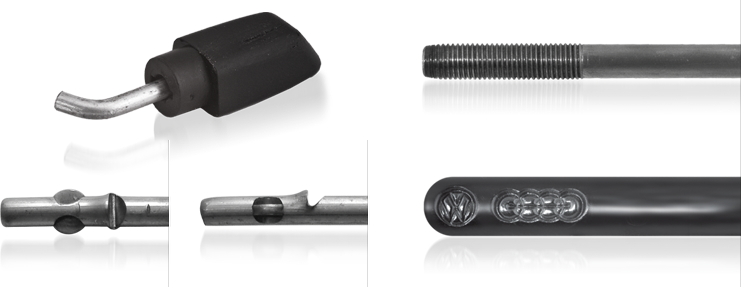
Notching | Marking |
Lug pressing | Punching |
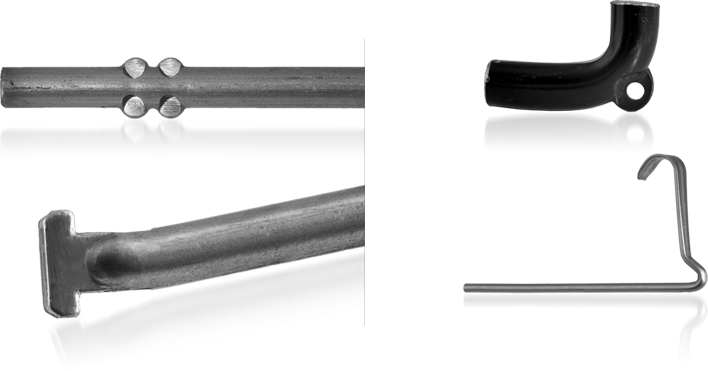
Cutting and deburring | Flattening in wire |
Typical diameter 1/4“ – 3/4“, up to 60 pcs./min. on one machining line, up to 35 pcs./min. when machining at several stations, any combination possible, series runs from 20,000 parts, finished part falling out, power requirement approx. 25 kW
Swaging | Cutting and stamping |
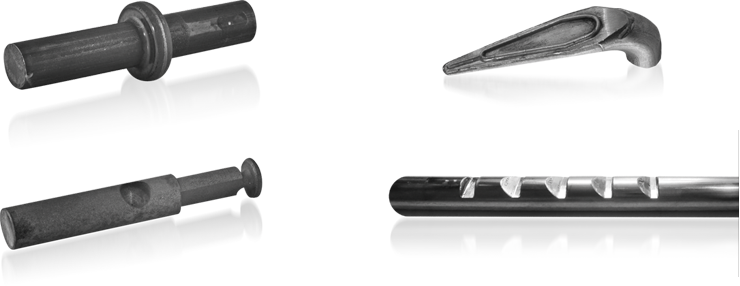
Milling | Broaching |
Flattening | Rounding | Flattening in wire 1 |
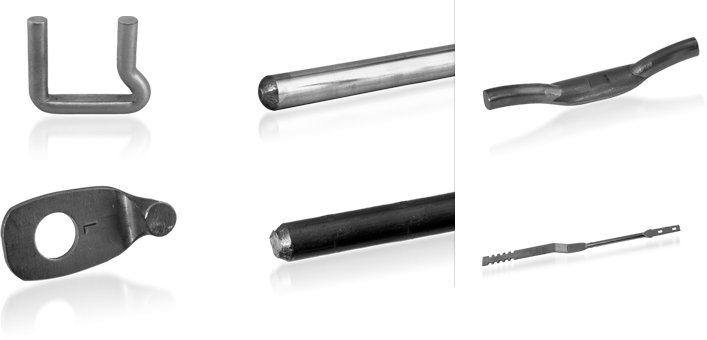
Cutting | Grooving in wire | Flattening in wire 2 |
Typical diameter 1/4“ – 3/4“, up to 60 pcs./min. on one machining line, up to 35 pcs./min. when machining at several stations, any combination possible, series runs from 20,000 parts, finished part falling out, power requirement approx. 25 kW
Wire machining
Metal wires are very useful to create different components for a wide variety of industrial segments. Of course, in order to transform a simple wire into the final component while achieving the desired results regarding design specifications, a series of forming process must be applied on the raw material.
Wire machining is part of those forming processes, and it refers to the various processes used to cut, size and shape the raw wire material into the desired result. Some of the most common machining processes applied on wire materials are thread cutting, notching, marking, lug pressing, punching, flattening, cutting and deburring, delivery and insertion (assembly).
Thread cutting
Also known as threading, it refers to the machining process used to create a thread such as on screws and nuts, or any other kind of metal part that requires a thread for its proper operation.
There are different methods to create a thread depending on the shape and material of the part, operational conditions and desired results, such as cutting, milling and rolling. In the case of wire machining, the most common methods are cutting, rolling and forming.
Notching
Notching, also known as notch pressing is a manufacturing process that requires some metal deformation and removal to achieve the expected result, as it is the case of many other machining processes.
To better understand what notching is, it is important to know that a notch can be defined as an indentation or incision on an edge or a surface. Therefore, notching is the process where a press is used to create such indentations or incisions on the metal part. Wire notching is frequently used to create not only one but a series of indentations that may be used as selectable levels, such as in the case of headrests that can be set at different heights.
Marking
Certain applications require the wire to show marks such as logos to identify the brand creating the part, part codification, and other specifications depending on the part and the manufacturer. These marks are achieved by means of stamping the mark on the wire with the help of a press and a custom die.
Lug pressing
A lug can be defined as a projection of an object by which it may be carried or attached to something. Therefore, lug pressing is the manufacturing process where a press is used to flatten the projection of the metal wire and to open the hole used by which it will be carried or attached.
A common application of lug pressing is the creation of cable lugs, which are necessary to secure the cables to their corresponding connections by means of screws and nuts or any other type of fastener.
Flattening
This forming process is usually applied to alter cross sections from round to a flat profile which is sometimes required to meet specific requirements and to comply with tight tolerances. This can be done manually by hammering the wire, but a better result is usually achieved by means of a press in a cold forming process.
A common use for flattening is to provide the possibility of joining a part with a round section (like a wire) to a flat part (like a sheet metal part) by means of screws or bolts. In this case, the wire is flattened at the ends to create a hole that will allow for the joint to be possible.
Punching
Punching is a manufacturing process which is used to remove a part of the material with a specific shape and specific dimensions by means of a punch press. The shape and dimensions are defined by the tool used, which is called the punch. It is usually performed on sheet metal or metal strips, but it can be performed on any part with a flat section like on a wire that has been previously flattened or lug pressed. It is commonly used to create holes with specific diameters for assembly purposes.
Cutting and deburring
Wires usually come in the form of coils, so they need to be cut to the size required. Moreover, some product designs require cutting the wire in different angles to achieve the desired shape. An undesired result from the cutting operations are the sharp metal extending beyond the edge, which is known as burr. So, deburring refers to the process of eliminating the burr to achieve a smoother edge and surface.
Swaging
Swaging of wire material is a forming process commonly applied to change the dimensions of the profile by forcing the wire into dies as a cold or hot working process. To achieve it, different methods are used, including extrusion through a die and the use of two or more rotary dies from the outside, both to reduce the diameter of a section or the entire part.
A common application of this process is creating collars with a round section, also known as collar swaging. Collars are used to provide locking power to a non-threaded part such as a bolt or to increase the locking power of threaded ones.
Cutting and stamping
Wires usually come in the form of coils, so they need to be cut to the size required. Moreover, some product designs require cutting the wire in different angles to achieve the desired shape.
In addition, some special marks or shapes are often required, and they are achieved by means of a press and a die in a stamping process.
Milling
Milling is a machining process where material is removed by means of a rotary tool that is fed into the workpiece in a specific direction. It allows to create different profiles on the wire to cover the specifications of the design with very tight tolerance values.
Broaching
This is a machining process where a toothed tool is used to remove material. It is commonly applied to create indentations that will be used as adjustment slots, like in the case of headrests. A key characteristic of this process is that it only requires one pass of the tool to remove the material, which makes it a very efficient process.
Rounding
As it was said before, wires come in the form of coils and they are cut to the desired size. After cutting the wire, it will have a very sharp edge and it will have some burr. With the rounding process, apart from removing the sharpness or deburring the edge, it is possible to give it certain radius and transform into a completely rounded end.
Flattening
This forming process is usually applied to alter cross sections from round to a flat profile which is sometimes required to meet specific requirements and to comply with tight tolerances. This can be done manually by hammering the wire, but a better result is usually achieved by means of a press in a cold forming process.
A common use for flattening is to provide the possibility of joining a part with a round section (like a wire) to a flat part (like a sheet metal part) by means of screws or bolts. In this case, the wire is flattened at the ends to create a hole that will allow for the joint to be possible.
Grooving
Grooving is a widely used cold forming process where a small portion of the wire is displaced radially. To achieve this displacement, the end of the wire is set between the roll set of a grooving machine. After the roll set is closed, compression and rotation are applied on the wire to form the groove around it, thus leaving a circumferential recess on the surface.
Wire Machining with Schmale Machinery
Traditionally, each process is performed independently requiring specific tooling (presses and dies) and operators for each of them. Of course, these requirements result in higher costs and reduced efficiency, which in turn means less productivity, a longer time to market and lower profitability.
To avoid all those negative aspects and improve the efficiency of the fabrication cycle, Schmale Machinery offers fully automated solutions which are extremely energy efficient, capable of integrating all the wire machining processes with any other processes required for the fabrication cycle.
These solutions include swage presses that can work in the pressure range from 24 tons to 300 tons, finger benders that can work with diameters from 2mm to 25mm and press units that go from 40 tons to 700 tons. Also, all units can be modified to custom specifications, including higher forces and customized dies. The majority of the pneumatic components used in our machines come from our partner Festo, while many electric components and automation, are provided by our partner Siemens. The great relationship with these outstanding partners allows us to also offer original spare parts even at short notice with a stock of more than 1 Million USD around the world.
All the machines designed by Schmale Machinery are capable of efficiently integrate the wire machining processes into a complex fabrication cycle. Special machines that are custom designed for a specific production situation can also be suitable for the machining of wires as part of a tailored production process.
If any or all of the wire machining processes are desired by a customer, Schmale firstly analyses the specific production situation and then develops the optimal production machine. As it is the case with all other production technologies, Schmale places the highest standards on the productivity and future viability of the machines created. This enables the wire machining processes to be integrated into the intelligent automation of various technologies.
The customer receives a modern, future-oriented and energy-efficient machine that has been precisely tailored to his requirements to produce complex components from wires in an economical and flexible manner.
The fabrication cycles obtained with Schmale integrated solutions only take a few seconds along the different stages to obtain the part ready for market, which clearly represents an enormous increase in efficiency and productivity and a significant reduction in the time to market, meaning that the profitability of your business will be higher. Moreover, series can run 20,000 parts or more depending on the specific part being produced.
Schmale Machinery has delivered hundreds of integrated and automated machines to serve a wide range of industries including the automotive industry, the household industry, the building industry, the public transportation industry and others, resulting in a large list of happy customers.
To have a better view of the process please refer to the pictures and videos.
If you are looking for an automated solution for wire machining, integrated with other processes required in your production cycle, or you have any further questions, please do not hesitate to contact us and we will gladly help you.