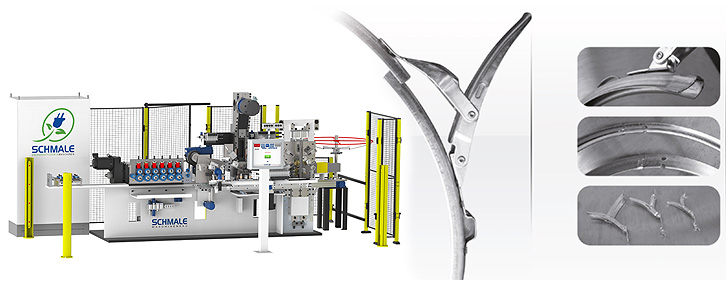
Dimensions: app. 23 ft x 10 ft and weight 20,000 lbs
Clamping ring machines
There are different types of clamping rings, which means there will be different ways of fabricating them. In general, most manufacturers have to deal with a series of operations to fabricate a clamping ring that may require a significant number of workers, machines and tools resulting in high operational costs.
On the other hand, there are different types of clamping rings because each of them is designed to cover a specific application. Among the most common applications there are sealing applications for the automotive industry, vacuum and pumping systems, piping installation and maintenance, connection fittings and drums closure.
Clamping rings for drums closure
Also known as drum locking rings, the clamping rings used for this application are usually an overlooked component despite how important they are.
Many times, drums are used to storage and transport substances that may be dangerous due to their corrosive or toxic nature. Therefore, ensuring a good closure to avoid leakage becomes crucial. Here is where the importance of the clamping rings becomes evident, as one way to make sure a drum is properly locked is making sure that the clamping ring is performing well. This means that the manufacturing process of this component must be done with the highest precision to meet the locking accuracy, strength and accuracy required.
The manufacturing process usually involves the following steps:
- Decoiling: the raw material (metal) is usually supplied in the form of coils, so it needs to be properly decoiled to start the manufacturing process.
- Profiling: the rings require a special profile that is formed to match with the surface of the drum cap where they are going to be installed.
- Bending and cutting: after the profile is formed, it needs to be bent and cut to form the ring.
- Widening the ends: this is done to allow for the clamp handle to be installed.
- Overlapping the ends: the ring is finally taken to its final form where the ends overlap.
- Welding the handle: the final component of the clamping ring is installed by welding it on the formed ring.
As it was explained before, traditionally, this process would take high operational costs and time to be completed.
However, the innovation of Schmale has completely changed this situation by introducing a clamping ring machine that fully automates the manufacturing process.
Integrating an automatic decoiler with a buffering system to control how the raw material is fed to the machine, a system to break the edges before the profile is formed, a series of rolls that help to keep the feeding of the material while forming the profile at the same time, to then bend it into the ring shape. After the ring is formed and cut, the machine counts on transfer systems that automatically take the ring and move it along the rest of the process for end widening, end overlapping and handle welding. The handles are automatically fed to the welding step to keep the continuous flow of the process.
The cycle takes 2.2 seconds and while one clamping ring is finished 4 more are already in the cycle (one in bending and cutting, one in ends widening, one in ends overlapping and one in welding handle). For a better view of the process watch the following video.
You can watch one of our clamping ring machines in action on our Youtube channel.
You can also see more specifications in the table below.
X2000NC The Sprinter |
Clamping ring machines The Specialist |
Special machines The Individualist |
---|
Drive | Servoelectric |
Strip | ![]() |
Pipe | |
Feed roller | ![]() |
Servo-hydr. feed-in | |
Buffer | |
Production speed | 0 to 28 pcs./min. |
Typ. wire diameter | |
Typ. strip dimensions | to 2″ x 1/8″ |
Free work surface | |
Transfer system | ![]() |
Stations max. | 6 |
Force functions | 2 |
Typical forces | 340,000 pound |
Servo axes | 8 |
Standard hydr. function | 0 |
Remote service | ![]() |
Weight approx. | from 20,000 |
Why Schmale Machinery
As it is the case with all other production technologies, Schmale places the highest standards on the productivity and future viability of the machines created.
The majority of the pneumatic components used in our machines come from our partner Festo, while many electric components and automation, are provided by our partner Siemens. The great relationship with these outstanding partners allows us to also offer original spare parts even at short notice with a stock of more than 1 Million USD around the world.
Schmale Machinery has delivered hundreds of integrated and automated machines to serve a wide range of industries including the automotive industry, the household industry, the building industry, the public transportation industry and others, resulting in a large list of happy customers.
Our customers can rely on a dedicated customer service department with remote service and on-site service, mostly provided within 24 hours.
If you have any further questions, please do not hesitate to contact us and we will gladly help you.