Service Packages
Together with the installation and set-up of our machines we offer a series of service packages for our customers to choose from.
Since we started building machines in 1965, we have seen our machines evolved, and we do several upgrades to all our machines every year, including electrical and control systems updates, and mechanical overhaul to overhaul guides, hydraulic aggregates, slides, bearings, and all the components that usually wear out over the time.
We offer these packages to our customers to ensure they keep up to date with the latest technologies and to help them evolve as we do.
Among the most common service packages we offer, there are:
- Inspections which are offered for all aggregates (slides, presses, etc.). Visual inspection is offered for free if you ship them to our plant. Deep and more technical inspections are charged at a flat rate and can be done periodically (annually, twice a year).
- Inspections which are offered for all machines (slides, presses, etc.). Visual inspection is offered at a low price. Deep and more technical inspections are charged at a flat rate and can be done periodically (annually, twice a year).
- Control systems modifications to update to the newest technology.
- General overhaul to increase system performance, replace all wearing parts and avoid cost-intensive stoppages.
Tailored service packages from the manufacturer ensure permanently fast and safe operation. Downtimes during control system modifications and general overhauls are minimized.
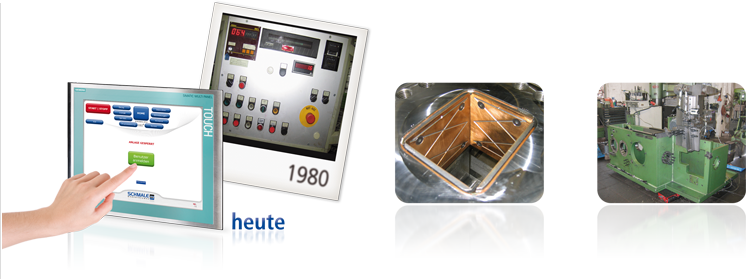
Control system modifications |
– Current technology with current options |
– Very good spare part availability |
– Avoiding cost-intensive stoppages |
General overhaul |
– Increase in system performance |
– Replacement of all wearing parts |
– Avoiding cost-intensive stoppages |
Tailored service packages from the manufacturer ensure permanently fast and safe operation. Downtimes during control system modifications and general overhauls are minimized.
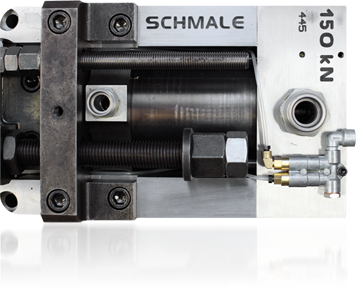
Slide inspection
– Tightness testing
– Checking of central lubrication
– Checking of guides
Why Schmale Machinery
As it is the case with all the production technologies offered, Schmale places the highest standards on the technical customer service provided. The customer receives a modern, future-oriented and energy-efficient machine that has been precisely tailored to his requirements to produce complex components in an economical and flexible manner and can also rely on a dedicated customer service department with remote service and on-site service, mostly provided within 24 hours.
Schmale Machinery has delivered hundreds of integrated and automated machines together with specialized and customized technical service to a wide range of industries including the automotive industry, the household industry, the building industry, the public transportation industry and others, resulting in a large list of happy customers.
Talking about our machines, we can highlight the fact that the majority of the pneumatic components used in our machines come from our partner Festo, while many electric components and automation, are provided by our partner Siemens. The great relationship with these outstanding partners allows us to also offer original spare parts even at short notice with a stock of more than 1 Million USD around the world.
To have a better view of the capabilities we offer, you can check our signature machines. Both the newly developed SPEEDMAX from Schmale and also the machines in the X2000 series can integrate the processes required into a complex production process to produce the desired metal parts from the materials described before. You can also see the pictures and the videos to see them in operation.
If you have any further questions, please do not hesitate to contact us and we will gladly help you.