Stage I | Stage III | Stage V |
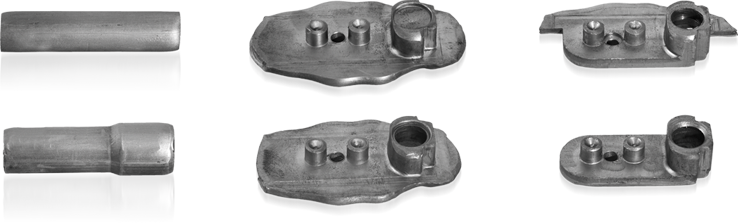
Stage II | Stage IV | Stage VI |
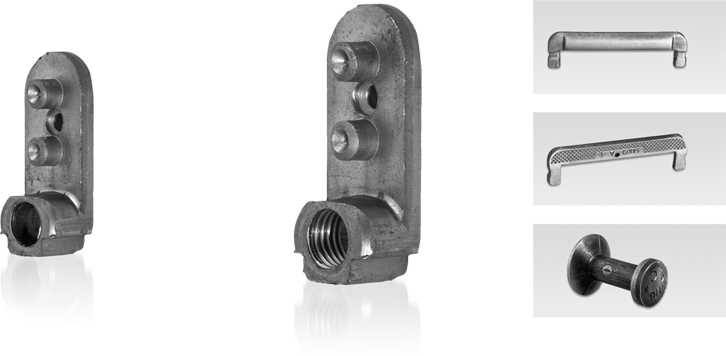
Stage VII | End stage
Diameter 3/8“, 2 sec cycle time, 30 pcs./min., flattening at 450,000lbs, finished part falling out including thread, power requirement approx. 20 kW
Cold forming
Cold forming is a metal forming process which consists in forging metal at room temperature. There are different ways to carry out this process, but basically it involves high pressure and a die to shape the metal.
Common features achieved by cold forming include flat sections and headed cylinders such as bolts and screws, which is why it is common to find the term cold heading related to the cold forming process.
How is cold forming performed?
As it was mentioned before, cold forming requires high pressure, usually obtained by means of a slide, a finger bender or a press, and a die. The metal is forced into the die at high speed with a blow of the punch. For the most complex shapes, it is usually necessary to use more than one die and more than one blow.
What is the difference between cold forming and other processes?
From the description given above, it is clear that the main difference with other metal forming processes, like hot forging or casting, is the fact that there is no need to heat or melt the metal. Another important characteristic of the cold forming process is that it usually increases the hardness and the yield and tensile strengths of the metal part formed.
Moreover, unlike machining, there is less or no scrap. This means a very high efficiency in the use of the material, thus resulting in a better cost-profit relation.
Cold forming with Schmale Machines
Of course, cold forming is usually just one step in the production cycle of a part, as many of the cold formed parts require other features that cannot be achieved during the cold forming process, such as the threads on cold formed screws, for example.
Traditionally, each process is performed independently requiring specific tooling and operators for each of them. These requirements result in higher costs and reduced efficiency, which in turn means less productivity, a longer time to market and lower profitability.
To avoid those negative aspects when performing cold forming combined with other processes on the same piece, Schmale machines provide fully automated solutions that integrate more than one process as required, including threading, heading and marking, allowing you to achieve a high level of efficiency and productivity.
The process begins with a wire with a diameter of up to 1″ fed into the tool set by automatic servoelectric feeders. Then the wire goes through the different processes where an arrange of automated units with their corresponding dies generate the expected results.
The entire cycle only takes a few seconds for each stage until the part is ready for market. This represents a capacity around 30 pieces per minute, which clearly represents an enormous increase in efficiency and productivity and a significant reduction in the time to market, meaning that the profitability of your business will be higher.
To have a better view of the process please refer to the pictures and videos.
If you are looking for cold forming solutions integrated in a fully automated production process, or you have any further questions, please do not hesitate to contact us and we will gladly help you.