Roll grooving 1 | Roll milling | Swaging of collar and head |
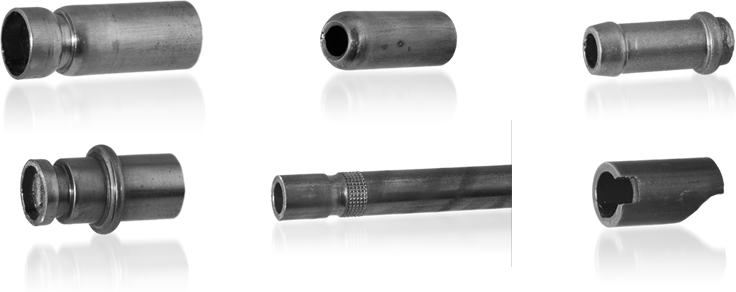
Roll grooving 2 | Knurling | Cutting with die insert |
Tapering 1 | Notching | Bending with die insert |
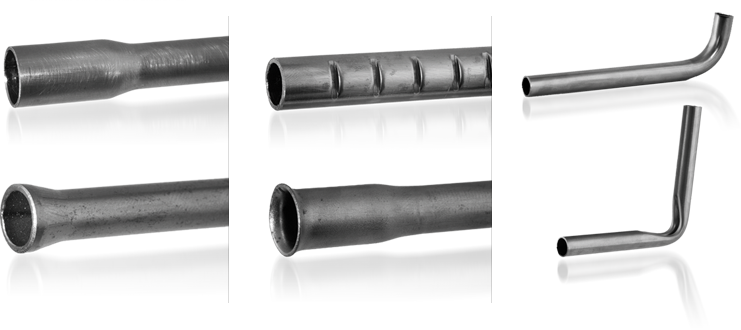
Tapering 2 | Belling | Bending with fold |
Typical diameter 1/4“ – 3/4“, up to 60 pcs./min. on one machining line, up to 35 pcs./min. when machining at several stations, any combination possible, series runs from 20,000 parts, finished part falling out, power requirement approx. 25 kW
Pipe machining
Pipe materials are very useful to create different components for a wide variety of industrial segments. Of course, in order to transform a simple pipe into the final component while achieving the desired results regarding design specifications, a series of forming process must be applied on the material.
Pipe machining is part of those forming processes, and it refers to the various processes used to cut, size and shape the raw pipe material into the desired result. Some of the most common machining processes applied on pipe materials are roll grooving, roll milling, swaging of collar and head, knurling, cutting with die insert, tapering, notching, belling, bending with die insert and bending with fold.
Roll grooving
Roll grooving is a widely used method to prepare pipe material for mechanical jointing. It is a cold forming process where a small portion of the pipe wall is displaced radially. To achieve this displacement, the end of the pipe is set between the roll set of a grooving machine. After the roll set is closed, compression and rotation are applied on the pipe to form the groove around the outside diameter, thus leaving a circumferential recess on the outside and an indent on the inside.
Swaging of collar
Swaging of pipe material is a forming process commonly applied on pipes to change the dimensions of the profile by forcing them into dies as a cold or hot working process. To achieve it, different methods are used, including extrusion through a die and the use of two or more rotary dies from the outside, both to reduce the diameter of a section or the entire part.
A common application of this process is creating collars on pipes with a round section, also known as collar swaging. Collars are used to provide locking power to a non-threaded part such as a bolt or to increase the locking power of threaded ones.
Knurling
Knurling a pipe consists in machining a pattern of straight, angled or crossed lines on the external surface of the pipe material for the workpiece by using specially shaped hardened metal wheels to improve its appearance and to provide a better gripping surface.
Tapering
Tapering is a forming process used on pipes to progressively reduce their diameter. It can be achieved by means of a two-die rotary hammering operation and swage presses. A great advantage of using swage presses to produce the tapered pipe material is that, as with any other swaging operation, there is no material loss and the structure of the metal remains mainly unaltered.
Other important characteristics of this pipe machining process is that there can be an increase in the length of the pipe, and it is also possible to achieve some wall thickening.
Notching
Notching, also known as notch pressing is a manufacturing process that requires some metal deformation and removal to achieve the expected result, as it is the case of many other machining processes.
To better understand what notching is, it is important to know that a notch can be defined as an indentation or incision on an edge or a surface. Therefore, notching is the process where a press is used to create such indentations or incisions on the metal part.
Bending with die insert
As the name itself suggests, this is a forming process where the pipe material is bent to the desired shape. However, a die insert must be used to give support to the inside of the material and prevent any collapse during the bending process. This practice allows to create bends at very tight radii on materials with very thin walls.
Pipe Machining with Schmale Machinery
Traditionally, each process is performed independently requiring specific tooling (presses and dies) and operators for each of them. Of course, these requirements result in higher costs and reduced efficiency, which in turn means less productivity, a longer time to market and lower profitability.
To avoid all those negative aspects and improve the efficiency of the fabrication cycle, Schmale Machinery offers fully automated solutions which are extremely energy efficient, capable of integrating all the pipe machining processes with any other processes required for the fabrication cycle.
These solutions include swage presses that can work in the pressure range from 24 tons to 300 tons, finger benders that can work with diameters from 2mm to 25mm and press units that go from 40 tons to 700 tons. Also, all units can be modified to custom specifications, including higher forces and customized dies. The majority of the pneumatic components used in our machines come from our partner Festo, while many electric components and automation, are provided by our partner Siemens. The great relationship with these outstanding partners allows us to also offer original spare parts even at short notice with a stock of more than 1 Million USD around the world.
All the machines designed by Schmale Machinery are capable of efficiently integrate the pipe machining processes into a complex fabrication cycle. Special machines that are custom designed for a specific production situation can also be suitable for the machining of pipes as part of a tailored production process.
If any or all of the pipe machining processes are desired by a customer, Schmale firstly analyses the specific production situation and then develops the optimal production machine. As it is the case with all other production technologies, Schmale places the highest standards on the productivity and future viability of the machines created. This enables the pipe machining processes to be integrated into the intelligent automation of various technologies.
The customer receives a modern, future-oriented and energy-efficient machine that has been precisely tailored to his requirements to produce complex components from pipes in an economical and flexible manner.