Feeders
Fingerbenders
Schedule an Appointment
Servoelectric drives
Schmale provides machines with an intelligent combination of technologies, and our concepts are as individual as your product to be manufactured. One of these technologies is servo-electric drives.
A servo-electric drive is an electronic device capable of receiving a signal from the control system to amplify it and power the servo-motor that will provide the motion required to the tool that is driving. Depending on the machine, the signals can represent current, velocity, torque, position and others.
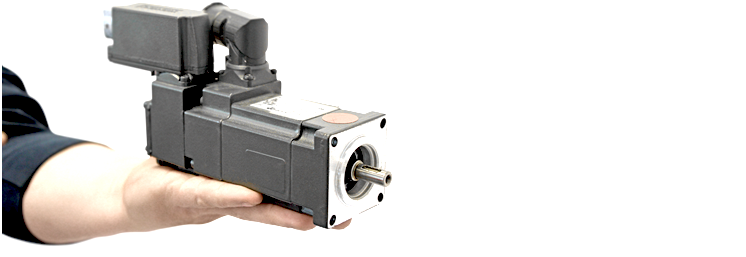
We use servos in many areas. Typical examples are feed rollers, thread rollers, rotary benders, bending sliders, presses, etc. The high flexibility and simple programming of our servo systems means that there are virtually no limits to the areas of application.
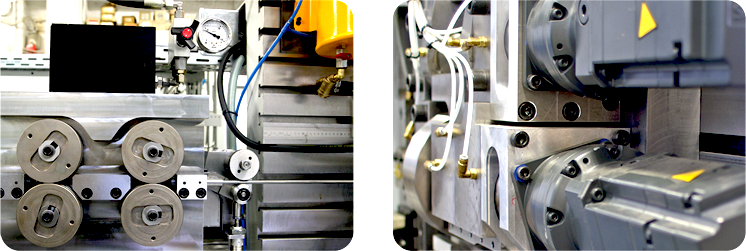
Servo-motors in punching – bending technology
The use of servo-motors in punching-bending technology has opened up new production opportunities. Although classically driven machines are able to operate at high speeds and produce correspondingly large unit quantities, the product diversity is limited.
In addition, mechanical machines can only be converted at high expenditures. The maintenance work is also time-consuming, as hoses must be refilled and inspected or cams must be machined.
In contrast, bending machines with servo-motors, such as the X2000NC produced by Schmale Machinery, enable considerably more flexibility with regard to product diversity and much lower maintenance requirements.
Machines driven by servo-motors also allow for a changed customer logistic strategy. While companies previously relied on large warehouses designed for long-term storage, today’s inventories are generally kept for shorter periods to save on costs. The consequence is orders of smaller quantity, which need to be completed on short notice and to which the producer must react with appropriate quickness, the quickness that can only be provided by machines such as the X2000NC and the newly developed SPEEDMAX.
Why Schmale Machinery
As it is the case with all other production technologies, Schmale places the highest standards on the productivity and future viability of the machines created. The customer receives a modern, future-oriented and energy-efficient machine that has been precisely tailored to his requirements to produce complex components in an economical and flexible manner.
The majority of the pneumatic components used in our machines come from our partner Festo, while many electric components and automation, are provided by our partner Siemens and others. The great relationship with these outstanding partners allows us to also offer original spare parts even at short notice with a stock of more than 1 Million USD around the world.
Schmale Machinery has delivered hundreds of integrated and automated machines to serve a wide range of industries including the automotive industry, the household industry, the building industry, the public transportation industry and others, resulting in a large list of happy customers.
Our customers can rely on a dedicated customer service department with remote service and on-site service, mostly provided within 24 hours.
To have a better view of the capabilities we offer, you can check our signature machines. Both the newly developed SPEEDMAX from Schmale and also the machines in the X2000NC series can integrate the processes required into a complex production process to produce the desired metal parts from the materials described before. You can also see the pictures and the videos to see them in operation.
If you have any further questions, please do not hesitate to contact us and we will gladly help you.